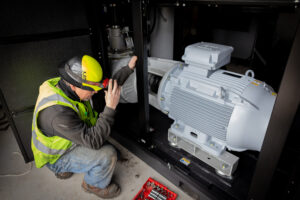
How to shrink energy bills, tap PPL incentives, and future-proof your plant’s compressed-air room
According to U.S. Energy Information Administration
Key takeaway: Upgrading to a premium-efficiency screw compressor returns dividends every hour it runs.
IE4 & IE3 premium-efficiency motors
Up to 4 % lower kWh per CFM than standard motors.
S-4 ships with IE4; C-series with IE3.
Low-RPM “SilentMount” design
Runs at ≤ 68 dB, protecting hearing and keeping multi-use buildings quiet.
Modular C-2 footprint
Fits tight Pennsylvania mechanical rooms, less than 10 sq ft at 11-22 kW.
Factory heat-recovery option
Captures as much as 72 % of motor heat to pre-warm water or space heat – ideal for PA winters. BOGE heat recovery brochure
5 + 5 extended warranty
Up to 10 years of predictable OPEX when serviced by an authorized partner (BOGE USA terms).
IE4 & IE3 motors
Up to 4 % better kWh/CFM than standard NEMA Premium.
S-4 series ships with IE4 motors; C-series uses IE3.
Low-RPM “SilentMount” design
Keeps noise ≤ 68 dB—ideal for multi-use buildings or OSHA-sensitive areas.
S-4 acoustics spec.
Modular C-2 footprint
Fits tight mechanical rooms common in legacy PA mills & food plants.
C-2 ≤ 10 sq ft at 11–22 kW.
Heat-recovery ready
Capture up to 72 % of motor heat to pre-heat water or space heat – great for cold PA winters.
BOGE heat-recovery kit brochure.
5 + 5 extended warranty
Predictable OPEX for a decade when serviced by an authorized partner, like CMC.
Based on data-logging studies across the Commonwealth, these profiles typically see payback inside 24 months:
Lancaster County precision machining
Pain point: High base-load CFM plus noise concerns.
BOGE edge: Low-RPM S-4 slashes both off-load kWh and decibels.
Ephrata / Lebanon produce packers
Pain point: Moisture in pneumatic lines during humid summers.
BOGE edge: Oversized after-coolers and Class 0 oil-free options keep lines dry.
Reading plastics extrusion
Pain point: 24 × 6 operation with big weekend swings.
BOGE edge: VSD control matches kW to real-time demand.
Pittsburgh entertainment venues
Pain point: Limited floor space and strict uptime for rides.
BOGE edge: Compact C-2 footprint plus cloud monitoring.
Bucks County pet-care formulations
Pain point: Rising electric rates and corporate CO₂ targets.
BOGE edge: IE4 motor + heat recovery cut both kWh and carbon.
Lancaster County precision machining
High base-load CFM, noise complaints in mixed-use parks.
Low-RPM S-4 cuts noise & off-load kWh.
Ephrata / Lebanon produce packers
Moisture-sensitive pneumatic lines during summer humidity.
Oversized after-coolers & optional Class 0 oil-free air.
Reading plastics extrusion
24 × 6 operation with variable draw on weekends.
VSD control keeps kW proportional to demand.
Pittsburgh entertainment venues
Limited floor space, strict uptime for attractions.
Compact C-2 + remote airstatus II monitoring.
Bucks County pet-care formulations
Rising electricity and sustainability targets.
IE4 motor + heat recovery knocks down CO₂ and utility spend.
These manufacturers are prime candidates based on load profile, kWh rate, and space constraints. If that sounds like your plant, read on.
Variable-speed compressors ≤ 40 HP qualify for prescriptive rebates (calculator built into PPL’s online tool).
Bigger systems (> 40 HP) can earn custom incentives paid per kWh saved—often covering 15 – 50 % of project cost.
Leak-survey & repair, storage tanks, zero-loss drains and heat-recovery kits are also incentivized.
Details, forms, and ZIP-code eligibility are covered in our companion article – PPL’S Electric Compressed Air Incentives- Compressor Maintenance
Peak CFM & pressure
Drives both capital cost and energy spend.
Rule: Peak demand × 1.1 for safety.
Duty cycle
Determines whether you need variable speed.
Rule: > 70 % load → choose a VSD S-4.
Oil-free or lubricated?
Food, pharma, and med-gas lines require ISO 8573-1 Class 0 air.
Rule: Class 0 needed → select BOGE HST oil-free.
Ambient heat & dust
High temps shorten component life.
Rule: ≥ 95 °F room → add ducted cooling or heat-recovery package.
Peak CFM & pressure?
Drives both cap-ex & energy spend.
Peak demand × 1.1 safety factor.
Duty cycle?
> 70 % load favors VSD.
S-4 VSD for variable shifts.
Oil-free vs lubricated?
Food/pharma need ISO 8573-1 Class 0.
Choose BOGE HST oil-free.
Ambient heat & dust?
High temps kill bearings & dryers.
≥ 95 °F → ducted cooling or heat recovery.
Legacy fixed-speed 75 HP compressor
425,000 kWh per year
$38,700 in electricity (@ 9.11 ¢/kWh)
BOGE S-4 75 HP VSD upgrade
370,000 kWh per year
$33,700 in electricity
$5,000 annual energy savings
≈ $6,000 PPL custom rebate *
Payback: under 24 months
Annual energy (kWh)
425,000
370,000
Electric cost (@ 9.11 ¢/kWh)
$38,700
$33,700
Annual savings
–
$5,000
PPL custom rebate*
–
≈ $6,000
Simple payback
–
< 24 months
* Rebate figure is an estimate based on $0.08 per kWh saved; final incentive requires PPL pre-approval.
Receive a free consultation.
Receive a side-by-side ROI report comparing current kWh vs. BOGE upgrade.
Let CMC handle PPL paperwork and schedule installation around your downtime window.
Send us an email at help@fixmycompressor.com, call us at 410-876-5141, or fill out the form below.
We’re looking forward to working with you. Whether you have questions about products or services, our team is ready to help.