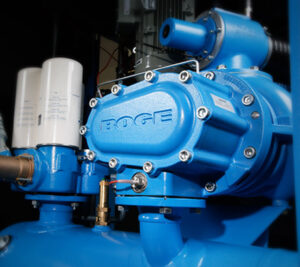
Industrial air compressors are the backbone of many industries, providing a continuous supply of compressed air to power tools and processes. However, like any machinery, they can occasionally encounter issues that can affect their performance or cause them to malfunction. By understanding these common problems and learning how to troubleshoot them, you can mitigate downtime and maintain productivity. However, there will always be times where expert assistance is necessary, and that’s Compressor Maintenance Company excels. This blog will discuss 7 of these problems and offer tips on how to troubleshoot them.
Overheating is a common problem that can affect an industrial air compressor. Overuse, inadequate ventilation, or issues with the cooling system can cause your compressor to overheat.
Firstly, check the environment around the compressor. Ensure that the compressor is not operating in an overly hot environment and that it has adequate ventilation. Also, check the cooling system for any obstructions or malfunctions. If the problem persists, it may require professional attention. This is the point where you might want to get in touch with Compressor Maintenance Company, whose team of professionals can help troubleshoot and fix more complex problems.
Oil leaks can occur in oil-lubricated air compressors. They can be caused by worn seals, loose connections, or a damaged oil filter.
Identify the source of the leak by checking the oil filter, seals, and connections. Tighten any loose connections and replace any worn seals or damaged filters. Regular maintenance checks can help detect and address oil leaks early before they become a major issue.
If your air compressor is not producing enough pressure, it can be due to several issues, including air leaks, blocked filters, or issues with the inlet valve.
If your air compressor is not producing enough pressure, it can be due to several issues, including air leaks, blocked filters, or issues with the inlet valve.
Excessive noise from your air compressor could indicate a mechanical issue. It could be due to worn bearings, loose parts, excessive wear, or a lack of lubrication.
Ensure all parts are securely tightened and that the compressor oil level is adequate. If the noise persists, it may be a sign of worn bearings that need to be replaced.
Motor failure can occur due to several reasons, including power supply issues, worn motor bearings, insulation failure, or overheating.
First, check your power supply to ensure it’s stable and meets the compressor’s requirements. If the motor is overheating, ensure the compressor is adequately ventilated and the cooling system is functioning properly. Worn motor bearings will need to be professionally inspected and replaced if necessary.
If your compressor will not start, it could be due to an electrical issue, a faulty motor, or an environmental issue such as freezing temperatures.
Check your power supply and ensure the compressor is properly connected. If the motor is faulty, it will need to be rebuilt or replaced. For temperature issues, ambient temperatures for hot environments may need to be adequately ventilated. Extremely cold environments may need to be heated.
If your compressor is consuming oil excessively, it might be due to a clogged scavenge system, a faulty oil separator, or improper oil levels.
Check and service the oil return/scavenge system. If the oil separator is faulty, it will need to be replaced. Also, ensure you’re using the correct type of oil and that the oil level is correct as per the manufacturer’s instructions. For more information on oil for air compressors, check out our comprehensive guide.
In conclusion, while these are common issues that can affect industrial air compressors, preventative maintenance is the best way to avoid these problems. Regular maintenance checks, perhaps facilitated by a knowledgeable partner like Compressor Maintenance Company, allow for early detection and correction of these problems before they escalate. Additional information on preventative maintenance and optimal compressor operation can be found here. Understanding your machine and its unique needs, referring to the manufacturer’s manual, and seeking professional help when needed can also go a long way in ensuring the optimal performance and longevity of your air compressor.
If you’ve exhausted these troubleshooting steps and the problem persists, it’s essential to contact a professional technician. They can provide a more in-depth diagnosis and appropriate corrective measures. The team at Compressor Maintenance Company is always ready to step in, equipped with the expertise to diagnose and rectify a wide array of air compressor issues. Attempting to repair significant issues without professional knowledge can sometimes lead to more extensive damage or unsafe operating conditions.
With the right attention to maintenance and troubleshooting, your industrial air compressor can continue to support your operations efficiently and contribute to the success of your industrial processes for many years to come. Remember, a well-maintained compressor isn’t just about preserving a machine; it’s about supporting your business’s productivity and operational efficiency. Trust your machinery to experts who understand your needs, like Compressor Maintenance Company, to ensure a smoother, more efficient production journey.
We’re looking forward to working with you. Whether you have questions about products or services, our team is ready to help.